| |
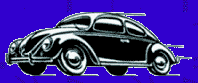
by Dave Conklin
I
have received a lot of enthusiastic comments from people who have seen the
American racing wheels on the "Cornpanzer" and really liked them. Many have
asked what it took to fit wheels such as this to a VW.
While it was not an easy swap, I feel that it was well worth the effort. I went
from "just another black 67 with polished EMPI repros.", to having a car that is
truly my own. I am going to try to review some of the major steps it took to
adapt these wheels. I will probably miss a detail or two. Keep in mind, these
tips will probably apply to adapting any style or size wheel.
First, let me describe the wheel to those of you who haven’t seen them. The
wheels are original Torque-Thrust "D" spokes. They were made in the early 70s
for road racing Porsches. The "D" designation refers to the arch in the spoke
that allowed extra clearance for disc brake rotors. These wheels are made from
Aluminum (also available in magnesium), and measure 15" x 7" with 4 ¾ inch
backspacing.
I had seen a pair of Americans on the rear of Mark Herbert’s infamous SSB in
June at the Classic, so I knew that the 7" width would work on the rear of a
beetle. The major problem was to be fitting them to the front.
To start with, I fitted factory "short" (pre 65) axles to the rear of the car to
allow for the bigger wheel. I used a standard 4 lug drum brake on the rear, and
had it re-drilled for the Porsche pattern. This is something that can be done by
any good machine shop, or you can order new drums already drilled from many
parts houses. With the 7" wheel on the rear with a 215/65 tire there is only
about 3/8’ between the tire and the spring plate. I have never had a problem
with rubbing, and they fit the fender just right.
At the front of the car however, things get a little more complicated. To start
with, I had Dave Pleasant at Quality Machine Co. in Dayton Ohio cut and narrow
the wheels down to 5" width. To do this, he cut 2 inches out of the backside of
the rim and heli-arced it back together on both the inside and the outside of
the rim for strength. This is an extremely critical operation. If this operation
is done improperly, the results would be an out of balance rim or even a broken
rim.
Next on the agenda was to narrow the front beam. I am using welded, dropped
spindles to lower my front end so this pushes the front track out 1 1/8 inch
wider than stock. ( 5/8" per side) This along with the different offset of the
American wheel meant that I would need to narrow the front axle beam 2 ½ inches
to make it all fit under the fenders. Since my car is a ball-joint car, I didn’t
need to make any body modifications. Narrowing the axle on a link-pin car will
be more complicated.
It is very important to sit down and measure everything out before diving in.
Different components such as disc brakes or cast spindles may change wheel
placement. High quality wheel spacers can be used to space the wheels out
slightly if desired. If spacers are to be used, source them from a high-end
wheel dealer. Porsche road racers often use spacers to dial in their front and
rear track. As long as you use good quality spacers, and don’t go any thicker
than approx. ¼" it should be ok.
Another problem I ran into was locating wheel studs. I found that Pep-boys and
NAPA retailers had a wide variety of press-in studs in both SAE and Metric
sizes. I would recommend that you buy your studs before you have the
drums/rotors re-drilled. This way the machinist knows exactly what size holes to
drill so that the studs press in securely. It is critical to make sure that your
lug nuts don’t bottom out on the drum/rotor before they tighten down on the
wheel. Also, there are different metric thread pitches, so make sure that the
studs you buy match your lug nut threads.
As mentioned earlier, these tips should help no matter if you are fitting
vintage American Racing wheels or the latest 17" Porsche Cup wheel. Anytime you
change anything in the wheel/suspension/braking area of your car it is important
to plan thoroughly, measure carefully, and use only the highest quality parts.
It may cost more initially, but you can’t put a price on your safety. Also, any
welding or fabricating should be left to the professional if you do not have the
tools or training to do it properly.
|